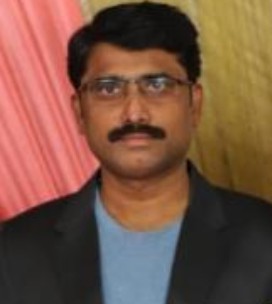
Q1.Can you share some key highlights from your extensive experience in Process Engineering and Simulation, and how it has evolved throughout your career?
- Process Design: Process engineers are in charge of creating new processes as well as enhancing current ones. Defining the objectives, selecting appropriate equipment and sizing, determining material flow, and developing process flow diagrams (PFDs), piping and instrumentation diagrams (P&IDs), and Heat & Material balance using process simulation software are all part of this process.
- Safety: It is critical to ensure the safety of employees, the environment, and the process itself. Through safety analyses such as Hazard and Operability Studies (HAZOP) and Process Hazard Analysis (PHA), process engineers must identify and reduce potential hazards and risks.
- Interdisciplinary Collaboration: To develop and optimize complicated processes, process engineers frequently collaborate with experts from diverse domains such as mechanical engineering, Instrumentation engineering, electrical engineering, Piping and materials science.
- Process Modelling and Simulation software (Aspen hysys, Aspen Plus, Chemcad, ASPEN EDR and Unisim): Process engineers build virtual representations of processes using modelling and simulation tools. This allows for the analysis, optimization, and prediction of process behavior of the equipment. Simulation software can assist engineers in determining the proper size and capacity of equipment such as reactors, heat exchangers, distillation columns, and pumps. Engineers can simulate the performance of many equipment alternatives and choose the one that best fulfills the project’s needs by entering process parameters and limits.
Q2. In your role as Sr. Manager at CH2M Hill, you were involved in FEED project execution. Could you elaborate on your responsibilities in this area and how it contributed to the success of the projects?
CH2M HILL- ABU DHABI (UAE) for Petrochemical plant – CHEMAWEYAAT (ADNOC) : FEED project roles and responsibilities are as follows:
- Heat & Material Balance (Aspen hysys), Development of PFD, P&ID and MSD
- Hydraulic Calculations and Process Equipment Design
- Process input/ coordination to other discipline
- Preparation of Basis of design and Operating, Control & safe guard Philosophy.
They are responsible for setting project goals, defining the scope, and establishing project timelines and milestones.
Client Interaction: They work closely with clients to understand their requirements, address concerns, and ensure that the project aligns with the client’s objectives.
Team Management: They oversee a team of engineers, designers, and other professionals involved in the FEED project. This includes assigning tasks, monitoring progress, and ensuring that team members have the necessary resources and support to perform their roles effectively.
Q3. You’ve had experience working in various locations, from India to the United Arab Emirates. How has this international exposure influenced your approach to Process Engineering and Simulation in different contexts?
- Cultural Sensitivity: Working in multiple worldwide locations exposes process engineers to varied cultures, work styles, and communication conventions. This experience can help them alter their communication and management techniques to be more culturally aware.
- Technological Adaptability: Travelling to different nations may need you to deal with different technologies and equipment. Process engineers with global expertise may be more adaptive and receptive to implementing new technology and best practices from various locations into their projects.
- Global Best Practices: Working overseas exposes process engineers to a wide range of industry best practices. They can learn from numerous ways and apply what they’ve learned to improve processes and solve problems in a variety of scenarios.
- Global Networking: Building a global network of professional contacts can help with collaboration, knowledge exchange, and career advancement.
International experience can broaden a process engineer’s perspective, making them more adaptive, culturally aware, and capable of dealing with problems in a variety of settings. It can also improve their ability to harness global best practises and effectively work with stakeholders from all around the world.
Q4. During your time at Ingenious Inc, you were a Process Simulation Trainer for CHEMCAD Software. Could you discuss the importance of continuous learning and training in the field of Process Engineering, and how it benefits both professionals and organizations?
- CHEMCAD Suite Proposal Engineering:
- Developing suggestions targeted to the requirements of engineering and operating firms in India.
- Demonstrating how the CHEMCAD suite may meet unique industry difficulties or requirements.
- The benefits and advantages of using CHEMCAD software in various engineering processes are highlighted.
- CHEMCAD Software Process Simulation Trainer:
- Approximately 40 training modules were delivered at various industry sectors (problem solving using simulation) and universities over a two-year period.
- Professionals and students are taught knowledge and expertise in process simulation using CHEMCAD.
- Assuring that participants understand the software’s capabilities and how to use it successfully for process engineering tasks.
- CHEMCAD Software Technical Support in Asia Pacific:
- Providing technical support to CHEMCAD software users throughout the Asia Pacific area.
- Helping users debug problems, optimise simulations, and answer technical questions.
- Contributing to the usability and efficiency of the product by obtaining user feedback and communicating it to the development team.
- Collaboration with the Sales Department:
- Working with the sales team to design and implement marketing strategy.
- Assisting with the identification of possible clientele and target markets.
- Following up with clients to meet their needs and answer any CHEMCAD software-related queries.
Q5. Can you provide some insights into the challenges and complexities involved in the Coal Gasification and Phenosolvan process monitoring, which you worked on during your tenure at Ingeniero?
The Coal Gasification and Phenosolvan Process Manufacturing Plant is located in South Africa, and we monitor plant performance from our Indian office by analysing data received from the facility.
1. Sensors and data acquisition:
Installed sensors and equipment to capture data at critical points in the process. Temperature, pressure, flow rates, chemical concentrations, and other variables can be measured using these sensors.
2. Data Transmission:
Implement a data transmission system to send sensor data to a centralized database or server. This can be done using wired or wireless communication technologies, depending on the location and infrastructure.
3. Validation and Quality Control of Data:
Implement data validation and quality control methods to assure the correctness and reliability of plant data. Checking for outliers, mistakes, and inconsistencies is part of this process.
4. Real-Time Monitoring:
Use real-time monitoring software to remotely monitor the plant’s functioning. Keep an eye on critical process parameters, equipment status, and safety systems.
To find deviations, compare current values to established setpoints and historical data.
5. Data Analytics:
To acquire insights into the process, use data analytics and visualization technologies. To find trends and abnormalities, use trend analysis, statistical analysis, and other techniques.
6. Reporting:
Produce regular reports that summaries process performance and variances. Charts, graphs, and key performance indicators (KPIs), tables, and recommendations for remedial measures can all be included in reports.
7. Historical Data Analysis: Analyzing historical data can provide insights into long-term process trends and performance. It can also help with predictive maintenance by recognizing wear trends on equipment. Implement machine learning models and predictive analytics to forecast process behavior and anticipate issues before they occur.
Organizations can improve operational efficiency, minimize downtime, improve product quality, and maintain compliance with safety by deploying a comprehensive remote process monitoring system. It also allows for data-driven decision-making and proactive maintenance and troubleshooting, which leads to cost savings and overall performance improvements.
Q6. In your current role as Assistant General Manager at Ingenero Technologies, you have listed Coaching & Mentoring as one of your skills. How do you mentor and guide your team members in the dynamic field of Process Engineering and Simulation?
Ingenero is establishing a new business entity in the Dynamic Simulation section to cater to the new Honeywell OTS and APM joint venture. Training and mentoring of young engineers and leaders for the effective completion of OTS and APM projects
Strategic Alliances:
Maintain and improve your relationship with Honeywell. Ascertain clear communication and agreement on project objectives and expectations.
Acquisition of a Project:
Create an acquisition strategy for OTS and APM initiatives. Take into account both existing Honeywell clients and future market potential.
Organizational Structure:
Create a dedicated team with the necessary mix of capabilities, such as experienced engineers, project managers, and support personnel.
Mentorship and training:
Create training programmes for young engineers and team leaders to ensure they have the skills and knowledge needed to succeed in OTS initiatives.
Project Management:
Implement strong project management systems to ensure that projects are completed on time and on budget. Track progress with project management software.
Quality Control:
Establish quality assurance and control procedures to ensure that your OTS and APM simulations are as accurate and reliable as possible.
Client Relationships:
Develop and maintain great client relationships by providing high-quality solutions and exceptional customer service.
Scaling and Expansion:
Plan for scalability by finding expansion and diversification opportunities in the field of dynamic simulation.
Reporting and Analysis:
Analyse project performance, client input, and financial indicators on a regular basis to make educated decisions and modifications.
Long-Term Goals:
Maintain a long-term vision and change your plan as needed to meet your business objectives.
Q7. Throughout your career, you’ve been involved in various stages of process development and improvement. Could you share a specific example of a project where you successfully optimized a process, and the impact it had on the organization’s operations?
- Setting up a new business entity inside Ingenero’s Dynamic Simulation department is a substantial task, but it can lead to a successful enterprise in the field of OTS and APM with careful preparation, smart collaborations, and a commitment to quality. (Ingenero Technologies (I) Pvt. Ltd)
- Digital Twin Technology: Virtual reproductions of physical processes or systems, known as digital twins, have grown in popularity. They make real-time monitoring, predictive maintenance, and better decision-making possible. (Ingenero Technologies (I) Pvt. Ltd)
- International experience broadens the toolkit of a process engineer by providing a broader range of experiences and viewpoints. It improves their adaptability, cultural understanding, and capacity to perform effectively in a variety of situations, making them more valuable assets to their organisations and clients in a globalised world. (CH2M HILL- ABU DHABI (UAE)
- Commissioning a continuous Styrene-Butadiene co-polymer (SBC) plant is a complex. (Apcotex Industries ltd)
- Special Project working with Leading consulting firm: Mancozeb (Pesticide) Technology Improvement group (Task Force) – Process evaluation, study and establish the issues related Agrochemical plant, Process engineering and equipment design (Indofil chemicals company)
Q8. In your Technical Officer/services/Marketing role at Apcotex Industries, you were responsible for Operations/Technical services/Marketing. How do you balance the technical aspects of Process Engineering with the practicalities of production and operations to ensure a smooth workflow?
- Participate in the resolution of major problems such as labor disputes, workforce staffing, material delivery and contract/subcontract administration
- Involved in shift production activities for the manufacture of Styrene Butadiene Rubber and Styrene Butadiene Latex by continuous process on a DCS operated plant using Emulsion Latex polymer as a raw material
- Commission of continuous Styrene – Butadiene co-polymer plant
- Technical service for continues styrene and butadiene polymerization
- To identify the training needs of the plant operation team and ensure the plant monitors staff training, and reports on training targets in the Performance Reports.
- Conducting market research or surveys for a new or existing product launch in the specialty chemicals industry can provide valuable insights into the Indian and global markets.