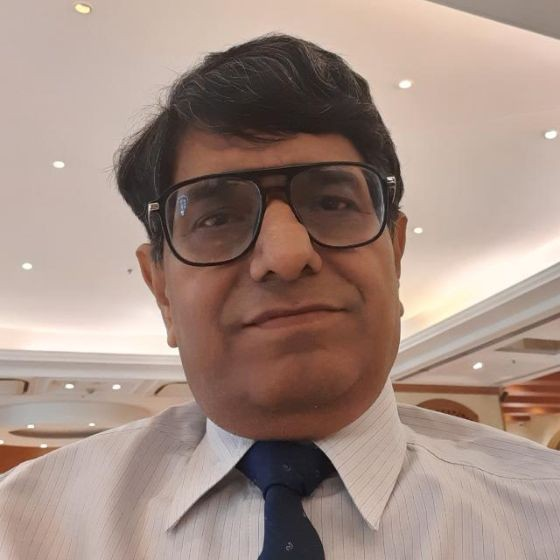
Q1. You have extensive experience in the textile industry, spanning various roles and functions? What initially drew you to this field, and how has your journey evolved over the years?
It was the summer of 1981, I got the result of the ZEE, where my rank was 1537. In the first counseling, I got a B. Pharma. In those days, none in the family had any realization of what a pharmaceutical specialist does. Nearest encounter we had with a pharmaceutical specialist was with a Medical Representative killing time in the waiting area of the clinic. It was not a very inspiring scene to be pursued as a career.
I was advised by a person in the textile industry that Textiles is the biggest industry after agriculture and the biggest mechanized industry. Since the demand for clothing is perpetual, this industry would always flourish. He also told me about my Alma mater TIT Bhiwani, a textile institute established by Birla Education Trust. Not known to many people but TIT (now TITS) is the only institute in the world with two big functional composite Textile mills of Birla management, just adjacent to the institute. I attempted their entrance exam and was selected.
Q2. How has your experience spanned almost the entire gamut of the textile industry?
God has been very kind to me, and He always kept on changing my learning and work domain to widen my learning horizon. When I look back on my journey in the field of more than 4 decades, I remember the words of Steve Jobs spoken at the convocation of Stanford university on the concept of Connecting The Dots.
It all started from the day I stepped into my alma mater, TIT Bhiwani. Design of curriculum and activities in TIT were elaborately designed. Almost everyday students used to spend some time in the factory. Curriculum was so designed that the entire syllabus of Textile Technology was taught till the third year of the institute. In the final year, we were taught about theoretical aspects only using research papers published in various international journals.
Since I had missed a proper engineering in an IIT narrowly, it was passion for me to learn about Textile Technology more than IIT Delhi students. The IIT campus was 3 KM away from my residence in Delhi. On weekends I used to come home and almost every Sunday used to study in their library. In one of those visits I came across a new technology being developed in Australian labs CSIRO where double yarn was directly made on the Ring Frame. I studied various aspects of this technology and this became the topic of my final year project. We group of three students modified the Ring Frame in the adjacent factory, made this yarn and fabric thereof. This led to my in-depth understanding of Spinning Technology.
When I was in second year, I helped my senior in his final year project in shaded Jacquard fabric manufacture. I was fascinated by the manner in which the warps and weft can be manipulated to create shades of different colors and their gradients. I wanted to choose fabric designing as my career.
But God had other designs. While we were passing out from the college, lot of composite mills in the country were closing due to combined effect of 1982 strike in Mumbai mills by Datta Samant, monetization of mill owners of vast real estate attached to the mills and policy of the then Central Government to promote disorganized power loom sector at the cost of big organized mills.
The classical textile industry did not seem very encouraging.
It was then, out of the blue there was an advertisement for the position of Management Trainees in JK Synthetics Ltd. Passing through group discussion and two rounds of interviews I was selected. It was a composite batch of 12 MTs coming from various fields of specializations.
My training in JK Synthetics & subsequent assignments in Sir Padampat Research Centre had a profound impact on my understanding of technical aspects of most synthetic fiber production, methodology of carrying out fundamental research and its upscaling, concepts of Quality management and statistical analyses and practical aspects of general management.
My institute prepared a comprehensive understanding of practical and research aspects in me related to the classical textile industry. Carrying out my own project and supporting the project of my senior made my in-depth understanding of Spinning & Weaving thorough. My stint with JK Synthetics made me get an in-depth understanding of fundamental research, applied research, quality management and process control in the field of most synthetic fibers prepared in India.
Q3. Would you like to elaborate how your stay in JK Synthetics impacted your career growth.
JK Synthetics was my second alma mater.
JK Synthetics, if I use terminology used in the current IT sector, was an excellent combination of hardware and software. It was the only place in the world with most varieties of synthetic filaments being made in one complex; Polyester Filament Yarn & Staple Fibre, Nylon Filament Yarn & Tyre Cord and Acrylic Staple Fibre. Icing on the cake was the presence of a well-established R&D Centre (Sir Padampat Research Centre) and very big Projects department, which had supplied technology and erected a few plants in India and Africa. So a complete set of research environment, operations facilities and technology development and transfer infrastructure were there.
Most importantly for 18 months we were trained in all these facilities by professors of IITs, IIMs, XLRI, various consultants and of course specialists in the plant.
If I use the same analogy as above, our Whole Time Director Mr Ramapati Singhania was Operating System. He had done his Post Graduation in HR management from Darden School of Business, University of Virginia.
He had a dream of implementing best HR practices in JK Synthetics. He empaneled our HR head supported by external consultants to design a generalist training programme for all of us. Besides this he had immense faith in the power of Quality Management. Twice, faculty from ISI Calcutta was brought to Kota to teach us in various aspects of statistical analyses in research, quality control and process control.
Though the company wanted us to be generalists, my passion was to do research. During the training period I used to spend 2-3 hours every day in the library of the R & D center and used to learn the functioning of various analytical instruments. Having been trained in all the products of the company, I could seamlessly do upscale research work at plant level.
Q4. As a Group Leader at Sir Padampat Research Centre, you conducted research in various fields, including waste recovery, polyester fibers, and acrylic fibers. Could you share a specific project or discovery from that time that had a significant impact on the industry?
It was in the R & D Centre, I met my principal mentor, head of R&D Centre, Dr ND Sharma. Whatever I did in my rest of the life in the field of research & scientific management was learnt under his tutelage. He taught me the rigorous process that must be followed in carrying out a scientific study and how to learn from so called failed experiments.
It was during those days, me and my associate Mr Atul Prakash Jain were given a project of development of technology for utilization of secondary polyester waste (Waste generated during waste recovery of polyester). Since day-to-day composition of the waste was varying, it was almost impossible to establish a workable research path.
Working on recovery of secondary waste became a passion for me and Atul. We used to work from 8:00 in the morning till 2:00 in the night – every day. There were a lot of failures, a lot of pitfalls. On days, it seemed there was a light at the end of the tunnel – later to realize that the tunnel actually did not open from the other end. After around 16 long months, we were able to make a successful process of converting it into Alkyd resin. It took another 6 months to upscale it in-house and later demonstrate and sell technology to an external alkyd resin manufacturer.
The efforts brought fruits. In the month of February 1994, we were awarded the Dr HC Srivastava award. Same year in the month of August, we received the NRDC award, which is given to scientists every year on Independence Day.
This work not only involved development of an independent route for the manufacture of Alkyd resins but also paved the way for handling wastes of the petrochemical industry, where composition is varying.
Q5. You were involved in designing the facilities of Technology Center for Reliance Industries. How has your previous learning and experience helped you in carrying out this assignment?
Me and Atul were invited to plan for the future Technology Centre to be brought up by Reliance Industries, in their recently bought plant of ICI on Thane-Belapur road.
It was then, a few dots of my previous academic and professional career connected.
The Design of Technology Centre involved planning of setting up a mini-textile plant spanning the entire gamut of the textile industry – From Spinning, weaving, knitting and of course synthetic fiber manufacturing.
I had developed a detailed understanding of the classical textile industry in my institute. JK Synthetics gave me exposure to all synthetic fibers, facilities required in a typical research and technology center planning for utilities and manpower to be associated with it..
Right manpower is key to the success of any venture and our task involved planning for manpower to be associated with each function and detailing skills, traits, competencies and experience required for each position. Under the guidance of Mr SY Nanal, advisor of Reliance Industries, we prepared a detailed document for the same.
Besides planning for the technology Centre, we developed many specialty polymers in a pilot plant, which was there in the old ICI plant.
Q6. Quality management appears to be one of your core skills. Could you elaborate on the importance of quality control and how it impacts the textile industry, especially in the context of your work?
There is an iconic song from the movie Shree 420 sung by Mukesh – Mera Joota Hai Japani. If you carefully notice the shoes of Raj Kapoor, they are torn off. It was in those days, when the euphemism Japani was an insult to a product – akin to Chinese a few years ago. Japanese commissioned Dr Deming to guide Japanese business and people the concept of quality management. Dr Juran also contributed a great deal in this endeavor.
History knows that the Japanese embraced quality management not in their minds but also in their hearts.
When legendary marathoner, Abebe Bikila, came to Japan for the Tokyo Olympics, the mayor of Tokyo himself led the people in cleaning the streets of Tokyo, making them completely free of the smallest possible stone. After all, the reigning Olympic and world champion was going to run on those streets – bare footed!!!. Japanese did not limit their quality management efforts to the rituals of certain practices, they habituated quality management in their hearts. It is no wonder that Japanese products are a hallmark of quality.
It is unfortunate that quality management in the Indian Textile Industry is relegated to only following mechanically some procedures and is concentrated only on setting of control and release parameters and segregating products.
There is another misconception: if we focus on maintaining quality, our costs go up. It is important to read the book by Philip Crosby, Quality Is Free. If we assess cost of conformance and cost of non-conformance, we would realize that efforts to maintain quality actually reduces cost of the product.
It is a sad state that textile products are sourced from India as a cheap destination rather than quality-producing destination. It’s a dream that in my lifetime I will see respect for our products in the same league as Japanese, Taiwanese, Korean or even Chinese products are being sold. We become a benchmark of quality and others strive to follow us.
Q7. During your tenure at PT Indorama Synthetics, you were involved in conceptualizing and commercializing specialty products across various divisions. Can you share some insights into the process of taking a product from concept to market, and any notable successes from that period?
To transform from commodity product manufacturing company to a specialty product manufacturing company takes transformation in every function of the company. Most companies just put a specialized R&D person or a small team and ask them to develop the product. The fact of life is that everyone from raw material procurement to production, quality control, marketing, sales and post sales customer support needs to be transformed.
It started in a similar fashion in Indorama also. But soon the directors of the company realized that product development is taking place at desired level but in the absence of supporting infrastructure we are not able to reap fruit out of the development. It was then the task of designing an integrated management structure was assigned to me.
In the integrated structure that was designed, the development activities were fragmented in three stages – pilot stage, Semi commercial stage and commercial stage. Roles were explicitly defined at each level of development for all related functions in such a way that responsibility slowly shifted from development team to regular operations & marketing team. There were few innovative steps taken in this structure.
To recruit and nurture quality R&D personnel from amongst the Indonesian professionals, Hay Mcbre competency model was modified to suit specific needs of the R & D job family and new competencies were identified and scales were developed for different levels of proficiencies.
Another step was creation of a specialized marketing structure. Most competent & versatile marketing professional of the company, with in-depth knowledge of regular and specialty products was assigned the job of leading the product promotion and seed marketing activities. He was supported by me in detailing to the customer how best we can utilize the specialty products on the customer’s machinery to unlock the hidden value. The information support was provided by another Textile Engineer, who had thorough understanding of digging out market information and used to advise management on future prices of principal raw materials. Just by way of reference, the first one is MD in a multinational company and second one is sector head in the biggest company in India.
Second important activity was assigning targets to each member of the marketing team for the number of new products referred to the development team, sales of specialty products and additional revenue realized out of them. It was numerically linked to their performance appraisal and increments.
From conceptualization to development to upscaling to commercialization, every step was monitored for techno-commercial viability. Before the first trial was started, Profit per day per machine was calculated. Even the trial parameters were evaluated on this line.
The net result was a spurt in development and commercialization of niche and ‘Specialty Commodity’ products. We were developing 4-6 new yarns every month. Technical success rate of the yarns at the customer level was more than 50% and commercial success rate was more than 20%.
At one point of time, 34% of the products of the company came from this category.
Q8. Your profile mentions your involvement in non-technical functions such as HR, business development, and marketing. How do these non-technical aspects intersect with your technical expertise in the textile industry, and how have they contributed to your holistic approach to your work?
It must be understood that no function in the company can operate in the silo. Like in normal operations all functions of the company intersect to bring out harmonious functioning of the company, so is the case with R&D.
Need of the organization was to integrate all sub functions related to specialty yarns individually and then synchronize them with principal functions of the company. So essentially there were three activities.
- Development of specialized R&D structure and systems within one divisions of the company
- Designing such structures and systems for all the systems of the company & carry out inter-divisional integration of the activities
- Integrating R&D structures and systems of each division of the company with that of principal manufacturing and marketing functions.
This is where all the dots got connected. My understanding of technical and marketing aspects of all the products of the company helped to design this Integrated Specialty Product Management Structure.
Biggest advantage of this integrated structure was the usage of shared resources of each division in terms of hardware, analytical instruments and trained manpower.
We had brought in innovation in the process of conceptualization, development, analysis, product promotion, branding and commercialization of the products. Our success in this endeavor was celebrated by the company and the tagline of Indorama was chosen to be INNOVATION EVERYEHERE.
Q9. You’ve served as President at Prag Bosimi Synthetics Ltd and were in charge of operations at their Guwahati factory. What were the challenges and highlights of managing plant-related activities, and how did it contribute to your overall experience?
Working with Prag Bosimi at the helm of the operations was a unique experience. It exposed me to those parts of the operations, which so far I had not experienced in my role as specialty product management specialist.
Biggest challenge in Prag Bosimi was managing its disadvantages pertaining to the location. Everything seemed to be on another planet, the raw material, market, trained manpower and even spares required to seamlessly run the plant.
Factory was situated in a remote village, 50 KM away from Guwahati with no facilities for the stay of engineers and support staff. There were no schools or decent medical facilities in the vicinity of the plant. So, the professionals with school going children used to avoid working there.
Even local workers preferred to work in western India, where job opportunities were abundant, and salaries were much higher. If a machine needed repair the technician was arranged from Silvassa or Surat, who would come by flight. Sometimes spares would reach the factory in 10-12 days.
So resource management was one challenge and managing the operations of the factory, in the absence of a skilled second or third line was another challenge. It got impounded in the functions, I had not worked.
But all this made me learn, which I could not have learnt in any other company.
Q10. In your current role as a Consultant at Filatex India Ltd, you’ve been involved in New Product Development across various types of polyester yarns. Can you share some of the most exciting projects or innovations you’ve worked on during this time?
Before I delve into exciting projects or innovations, it is pertinent to mention that the classical textile industry is a relatively low-tech branch of knowledge. In general there are excitable innovations and activities are linked to tweaking existing products, here and there and bringing out new features which can help our customer in improving performance on his machinery or end user experiencing some unique feature.
Some of the products which have been developed here are
- FlexiFIL: A yarn giving stretch to the fabric without Spandex, rubber or modified polyester polymer
- FILaspun: A yarn with touch and softness of Egyptian cotton.
- KoolFIL: Moisture management yarn; Keeps clothes dry and odour free
- WarmFIL: Very lightweight warmth giving yarn
- WoolFIL: Look and touch of woolen or worsted fabric
- FILllory: Netlike fancy effect in fabric
- FILus: Ultra low shrinkage yarn
All these modifications have been carried out on hardware designed to make the commodity product using regular polyester polymer. If we club it with specialized polymer, more exciting and innovative products can be produced.